The furnace is indeed the heart of a glass manufacturing facility, playing a crucial role in transforming raw materials into molten glass. The batch materials used in the process are carefully selected based on the desired color of the final product—whether it be white, brown, or green glass—as well as the specific type of glass being produced, such as bottles, crystal, or float glass. Cullet, which is recycled glass from production waste, is also incorporated to enhance efficiency and reduce raw material costs.
Furnaces are constructed in various configurations, including sections like M.E (Melting End), W.E (Working End), and F.H (Forehearth), and they come in different sizes and tonnages tailored to the factory's production capacity. The design can vary depending on the manufacturing process, utilizing either Sideport or Endport configurations and incorporating either recuperators or regenerators to optimize energy efficiency.
The production process begins with the introduction of raw materials through the batch charger into the furnace's Doghouse, where they are subjected to extreme heat—approximately 1550 degrees Celsius—to facilitate melting. After this initial melting phase, the glass moves through the Refiner for purification, ensuring that any impurities are removed. Subsequently, it passes through the Forehearth channel, where its temperature is carefully reduced and stabilized before it is finally ready for shaping into bottles or other glass products. This intricate process highlights the importance of the furnace in achieving high-quality glass production.
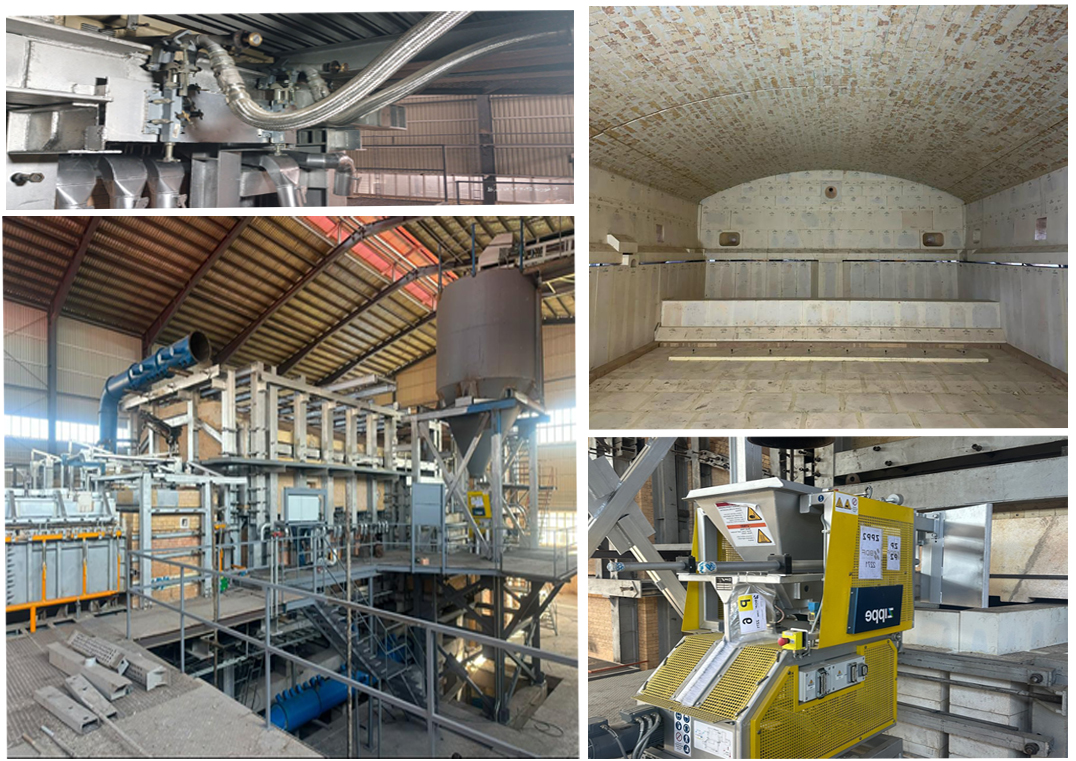